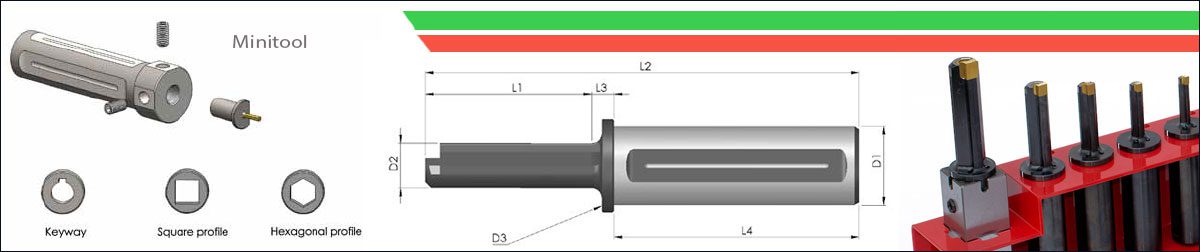
The REV Tools
Made with quenched and tempered tool steel
The REV Broaching Tool is made with quenched and tempered tool steel. The section that houses the insert is hardened to 58/60 HRC, making it very resistant to compression and guaranteeing the tool a long service life. The REV Broaching Tool features 3.5mm holes for the forced supply of coolant liquid which, in addition to lubricating and cooling the insert, are used to extract the chips, produced through broaching or slotting, in a blind hole. The tool is available in two shank diameters (25mm and 32mm). Two tool lines are available for each shank diameter: standard and long (identified by the suffix “L” in the code). We also produce special tools and inserts, based on specific customer demands, and provide a quick turn-around of inquiries and orders. The REV Broaching Tool differs from similar tools currently on the market by its patented eccentric bushing that completely eliminates symmetry errors. This bushing was provided so that any lathe without a Y-axis can perform processing in perfect alignment with the workpiece. The REV Broaching Tool guarantees low impact on the machine tool bearings. To date, none of the thousands of REV system users has reported issues of breakage or unusual wear caused by broaching on the CNC. Based on tests carried out by REV, the cutting force for executing key housings with a 20mm width, for example, is comparable to the cutting force required for a common hole with a 14mm diameter.
The REV Broaching Insert and Tool can cut in either through or blind holes with or without a relief groove or a 0.2mm x 45° chamfer. Ideal for both single and timed or multiple cuts. Inserts and tools are available to cut, square, hexagonal, pentagonal holes and involute teeth, as well as keyway slots, PTOs and special shapes. The maximum processing depth is 200mm, with standard tools. When it is necessary to execute considerably large key housings, it is good practice to perform the operation in two steps: a roughing phase to remove approximately 50% of the material, and a finishing phase to achieve the required size. Accordingly, you avoid excessive stress to the tool, and you improve precision and surface finish at the same time.
The materials that can be processed are;
• High and low-alloy low-carbon steel, and non-alloy steel
• Stainless steel, quenched and tempered steel, cast iron, AVP
• Non-ferrous materials such as aluminum alloys and titanium
• Copper alloys, bronze, and engineering plastics